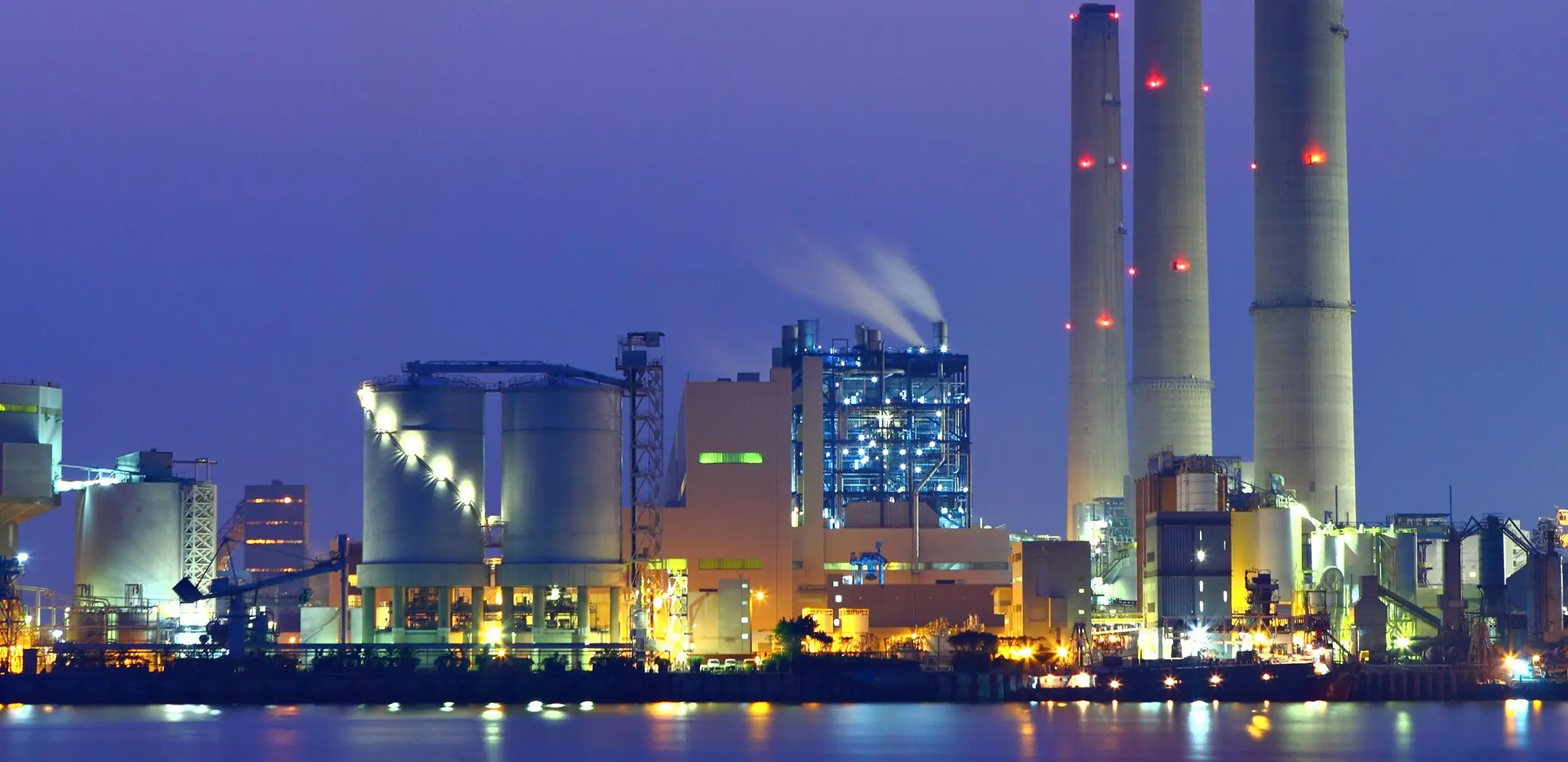
Order to Indonesia
Reference / Conventional and Nuclear Power Engineering
Order to Indonesia: High-Pressure Gate Valves DN 600 weighing 6,5 t. In 2016, Vexve Czech unit won a contract to supply two S43 DN 600 PN 250 high-pressure gate valves to Indonesia. The gate valves were designed for high service parameters and operated by a spur gear operator and electric actuator made by AUMA.
One valve was 3.3 metres tall and included the attached control, weighing a significant 6,500 kilograms.
The service fluid is steam with a pressure of 121 bar and a temperature of 530°C. The gate valves should be connected to a piping made of ASTM A335 P91 (later referred to as P91) with dimensions of 610 x 36.53 mm in the pulp and paper mill.
We carefully considered how to achieve the lowest possible price while meeting safety requirements and customer specifications from the start of the order preparation. Due to the high cost of P91 material, we opted to create a gate valve using a combination of two materials.
Specifically, we selected 14MoV6-3 for the main body and extension piece, while reserving the use of high-grade steel P91 solely for the valve body ends that will be directly connected to the piping. The main body forging weighed 6,800 kg before machining, but only 2,800 kg after. This means that most of the steel material became scrap in the form of metal chips.
We therefore suggested using a different grade of steel (14MoV6-3) that would meet the service requirements and be more economical. The extension piece, which is also made of 14MoV6-3, was welded to the body to install the bonnet. Finally, the end connections made of P91 were welded to the body. The weight of the entire body weldment was 4,230 kg.
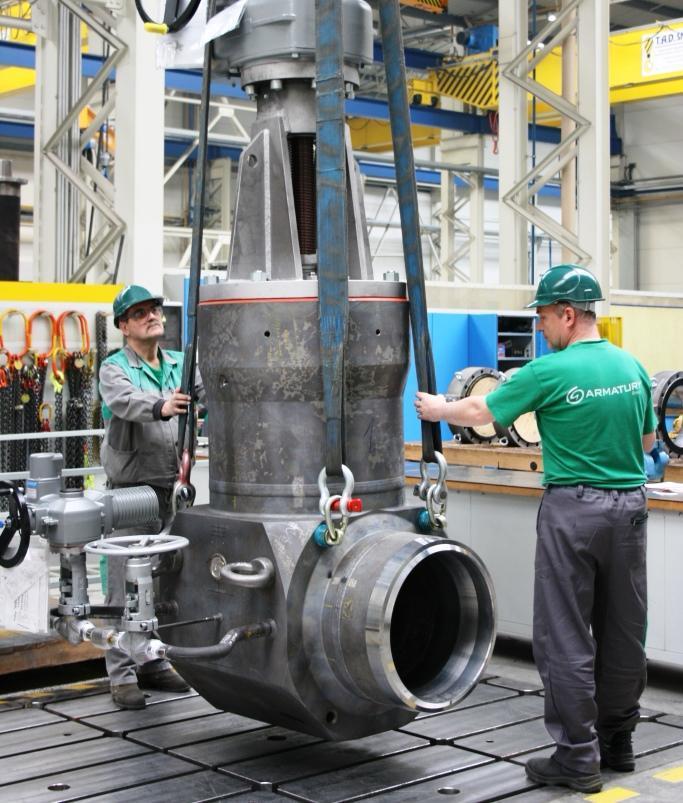
Heavy-Duty Gate Valve
The gate valve is a heavy-duty valve. Therefore, other parts of the valve are also designed to be robust. The seats and wedge gate have hard faced seating surfaces made of Stellite 6, which is the most suitable material for the fluid being transported.
The body-bonnet joint is a pressure seal joint sealed with a profiled graphite ring. To protect against pressure increase in the valve body cavity, a double bypass system with a nominal size of DN 40 is provided. The shell strength tests were carried out on the gate valve by European Standards, and the results were satisfactory.
The gate valve's large size presented various production challenges. These included handling different parts, machining individual components, qualifying welding procedures and welders, and preparing fixtures for plasma hard facing of seating surfaces and assembly. To overcome these challenges, careful planning and execution were necessary.
New Technology Used
To enhance the welding of 14Mo6-3 steel, we utilised a new technology for automatic submerged arc welding with tubular cored wire and basic filling (international welding process number 125).
The weld has a diameter of 780 mm and a thickness of 67.5 mm. This technology allowed us to reduce the welding time from the initial 14 hours to just 6 hours. All welding was carried out at a temperature range of 200-250°C.
The furnace was used to preheat the P91 and 14MoV6-3 materials for automated and manual welding. Heating pads with resistance heating were used for the process. The quality of all welds was examined using radiographic and magnetic particle examination methods. This part of the production process was challenging for both pre-production personnel and production workers, requiring utmost concentration.