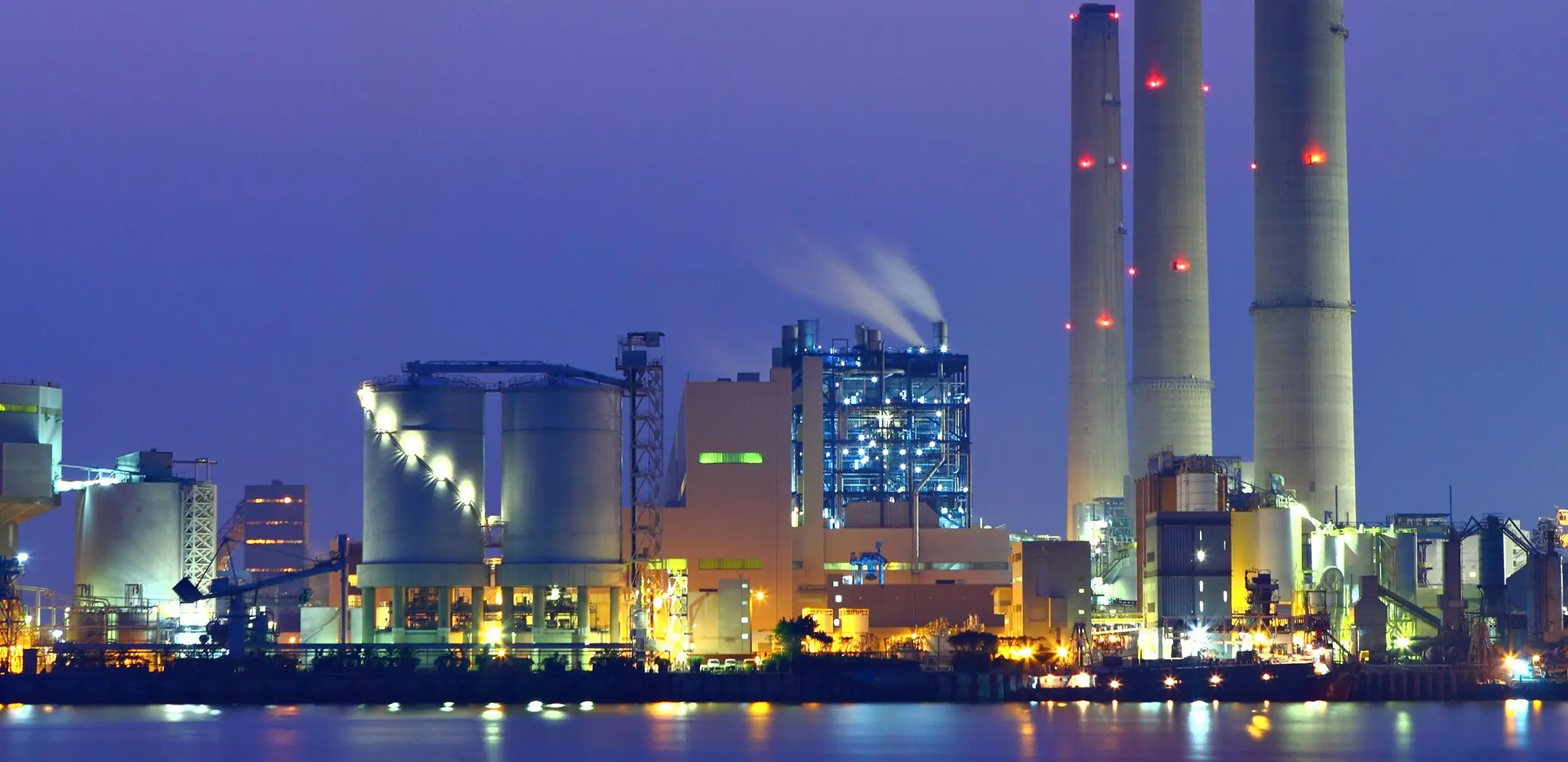
Bestellung für Indonesien
Referenz / Nukleare und konventionelle Kraftwerke
Bestellung für Indonesien: Hochdruckabsperrschieber DN600 mit einem Gewicht von 6,5t. ARMATURY Group hat zwei große DN600 S43 Hochdruck-Schieber nach Indonesien geliefert. Die 3,3m hohen Armatuen wogen 6,5 Tonnen.
Im Jahr 2016 gewann ARMATURY die Auschreibung für zwei DN600 PN250 S43 Schieber für die Papierindustrie. Die Schieber sind auf sehr anspruchsvolle Betriebsparameter ausgelegt worden und werden von einem elektrischen AUMA Antrieb angetrieben. Der Dampf hat eine Temperatur von 530°C und 121 bar. Die Schieber werden an eine Rohrleitung aus dem Material ASTM A335 P91 und mit den Abmessungen von 610 x 36,53mm angeschweitßt.
„Von Anfang an Stand Qualität, Sicherheit und Preis im Fokus dieser Ausschreibung. Um diesen Anforderungen optimal gerecht zu werden, wurden zwei Materialien verwendet. Der teurere P91 wurde nur für die Anschweißenden verwendet und der etwas günstigere 14MoV6-3 für Gehäuse und Spindelverlängerung. Dadurch konnten die Kosten bei gleichbleibender Qualität signifikant reduziert werden. Das Gehäuse wog vor der Bearbeitung 6,8 Tonnen, danach nur noch 2,8. Aus diesem Grund empfohlen wir den Schieber aus zwei verschiedenen Materialien zu fertigen. Die Spindelverlängerung, ebenfalls aus 14MoV6-3 wurde wie die Anscheißenden aus P91 an das Gehäuse angeschweißt. Das Gewicht dieser Armatur ohne Antrieb wiegt alleine 4,3 Tonnen.
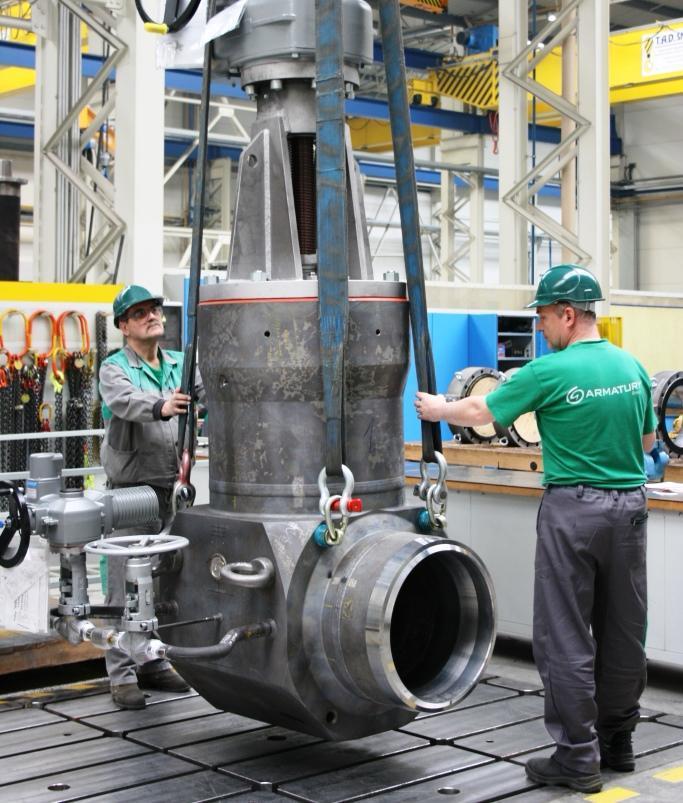
Hochleistungsschieber
Der Schieber und all seine Bestandteile sind als Hochleistungsarmatur konstruiert und produziert. Die Sitzoberfläche am Gehäuse und Keil sind aus Stellit 6, welches das geeignetste Material für Dampf ist. Der selbstdichtende Verschlussdeckel ist mit einem profiliertem Graphitring ausgestattet. Als Überdrucksicherung für den Totraum gibt es außerdem zwei Beipässe mit DN40. Der Schieber wurde nach EN12266 mit 375 bar geprüft.
Durch das enorme Gewicht und Größe der Armatur gab es zahlreiche Herausforderungen in der Produktion, wie z.B. Bearbeitung, Schweißen und Handhabung um nur einige zu nennen.
Neue Schweißtechnologie im Einsatz
Um die Verschweißung von 14MoV6-3 zu verbessern wurde ein neues Schweißverfahren verwendet. Das Unterpulverschweißen mit Fülldrahtelektrode, entspricht dem internationalen Schweißverfahren 125. Die Schweißnaht hat einem Durchmesser von 780mm und 67,5mm Dicke. Durch diese neuartige Methode konnte die Schweißzeit von 14 Stunden auf nur 6 Stunden reduziert werden. Alle Schweißlagen wurden bei einer Temperatur von 200-250°C aufgebracht. Um diese Temperatur sicherzustellen wurden alle Teile, P91 und 16MoV6-3 im Glühofen vorgewärmt und dann manuell verschweißt. Um die Temperatur über einen längeren Zeitraum zu halten wurden Heizkissen verwendet. Die zerstörungsfreie Prüfung der Schweißnaht wurde anhand einer Röntgen- und Magnetpulverprüfung durchgeführt. Die hohen Temperaturen waren eine große Herausforderung für das Prüf- und Schweißpersonal.