Successful cryogenic test of ball valve K92. C
The threat of cutting off Europe from gas flowing through pipelines from the East is fueling increased interest in liquefied natural gas, also known as LNG. In addition, it is considered a possible ecological and more cost-effective alternative to diesel.
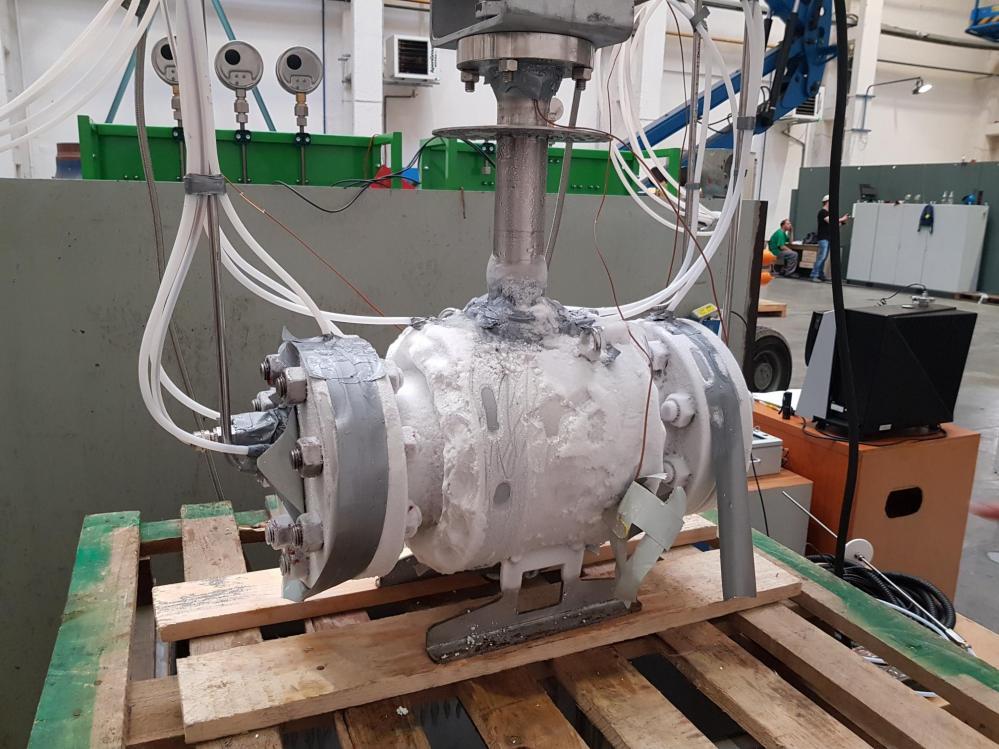
Cryogenic ball valves are used in the storage, distribution and transport of LNG, with the production and testing of which they have great experience in ARMATURY Group. On 10 - 13 May, a successful cryogenic test of the ball valve K92.C NPS 8 Class 300 took place. This ball valve can be one of the components for the production and transportation of liquefied natural gas.
100% tightness is the basis
The ball valve with a new type of seats has been tested according to BS 6364. These standard states that under all operating conditions within the maximum permitted temperature and pressure range, there must be 100% tightness of the body and seal, and there must be no leakage of medium from the piping system into the surrounding environment.
Under cryogenic conditions, a leak in the seat is allowed, with a maximum of 100 cubic millimeters per second multiplied by the internal diameter of the valve. After cryogenic application, i.e., under standard non-cryogenic conditions, the valve must again be 100% tight, even in the seat. To achieve this, 100% tightness must occur after a certain period, during which the temperature of the valve itself will increase from cryogenic to ordinary.
After installation, pressure tests were carried out at room temperature. The ball valve was tested with compressed helium for overpressure and tightness of the seats. All tests passed; the tightness was with zero leaks.
Testing
The cryogenic test was carried out according to standard BS 6364 by immersing the ball valve in a liquid nitrogen bath at -196 °C and by exposing the ball valve to a defined internal overpressure with helium. The measuring device then monitored possible helium leaks in the saddle parts and in relation to the external environment. The ball valve sealed with zero leaks in the seat test up to -150 °C, at -196 °C the worst result was 170 ml, which is seven times better than the BS 6364 standard, which determines a leakage of up to 1200 ml! When heated to 20 °C, the ball valve was again tight, with zero leaks.
The result of the technically and time-consuming test was a great conclusion: the cryogenic ball valve passed the test with a satisfactory result. At ARMATURY Group, they are thus prepared for new challenges in the supply of ball valves for cryogenic applications, such as liquefaction of natural gas to LNG.
For more information:
Jan Plaček, designer
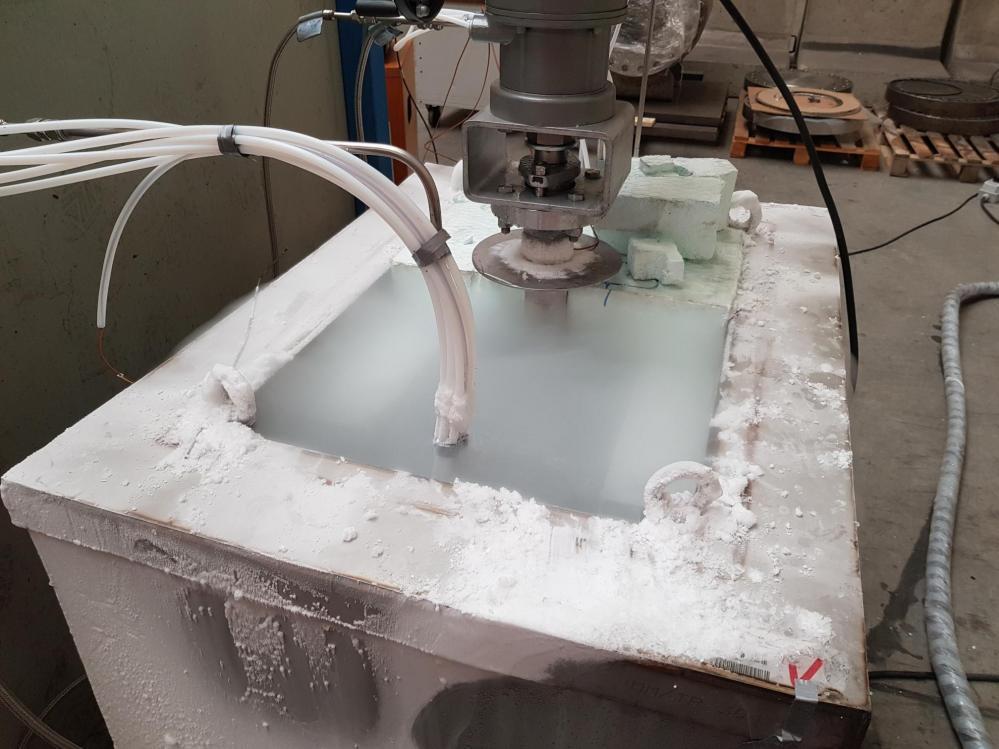
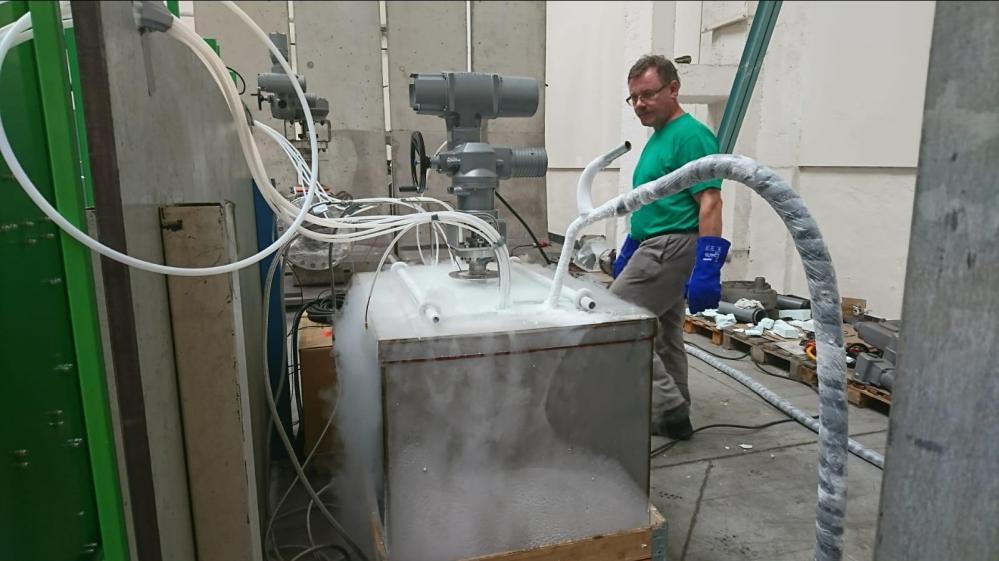
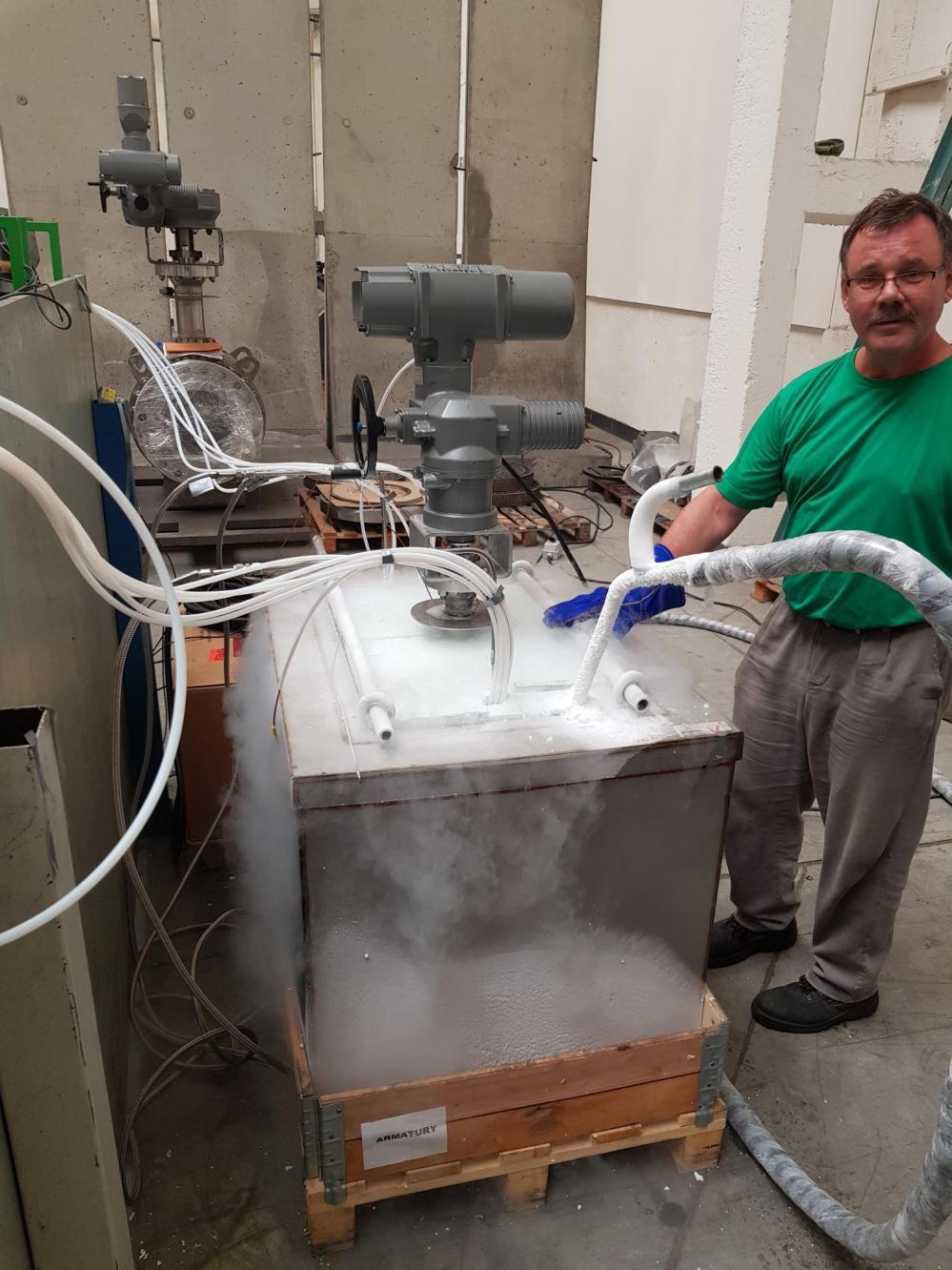
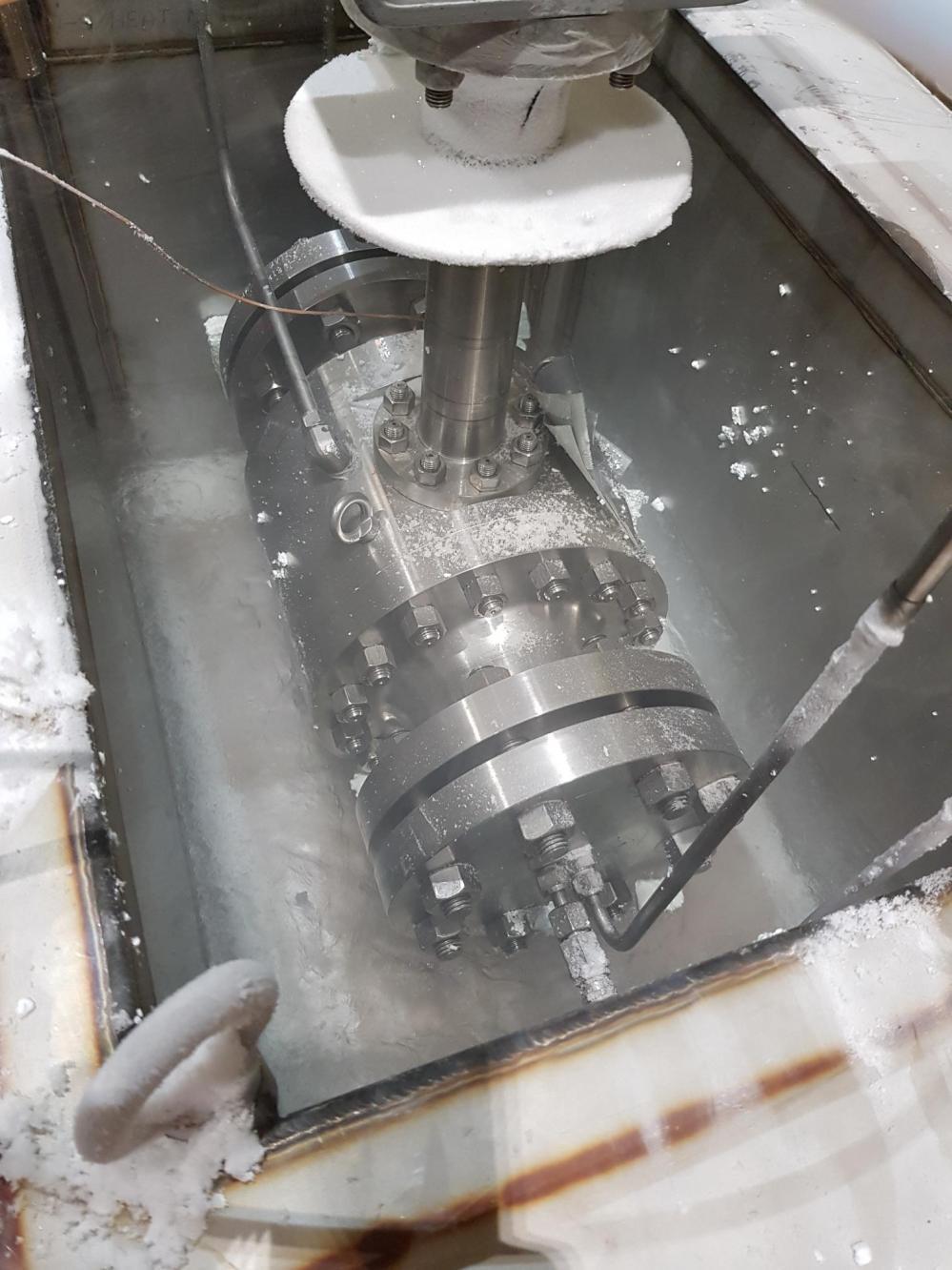